Anatomy of a mobile dust collector
Onsite Dust Collectors use equipment manufactured exclusively by Grydale - a world-renowned manufacturer of high-quality, technically-advanced dust collectors. Here's work they work...
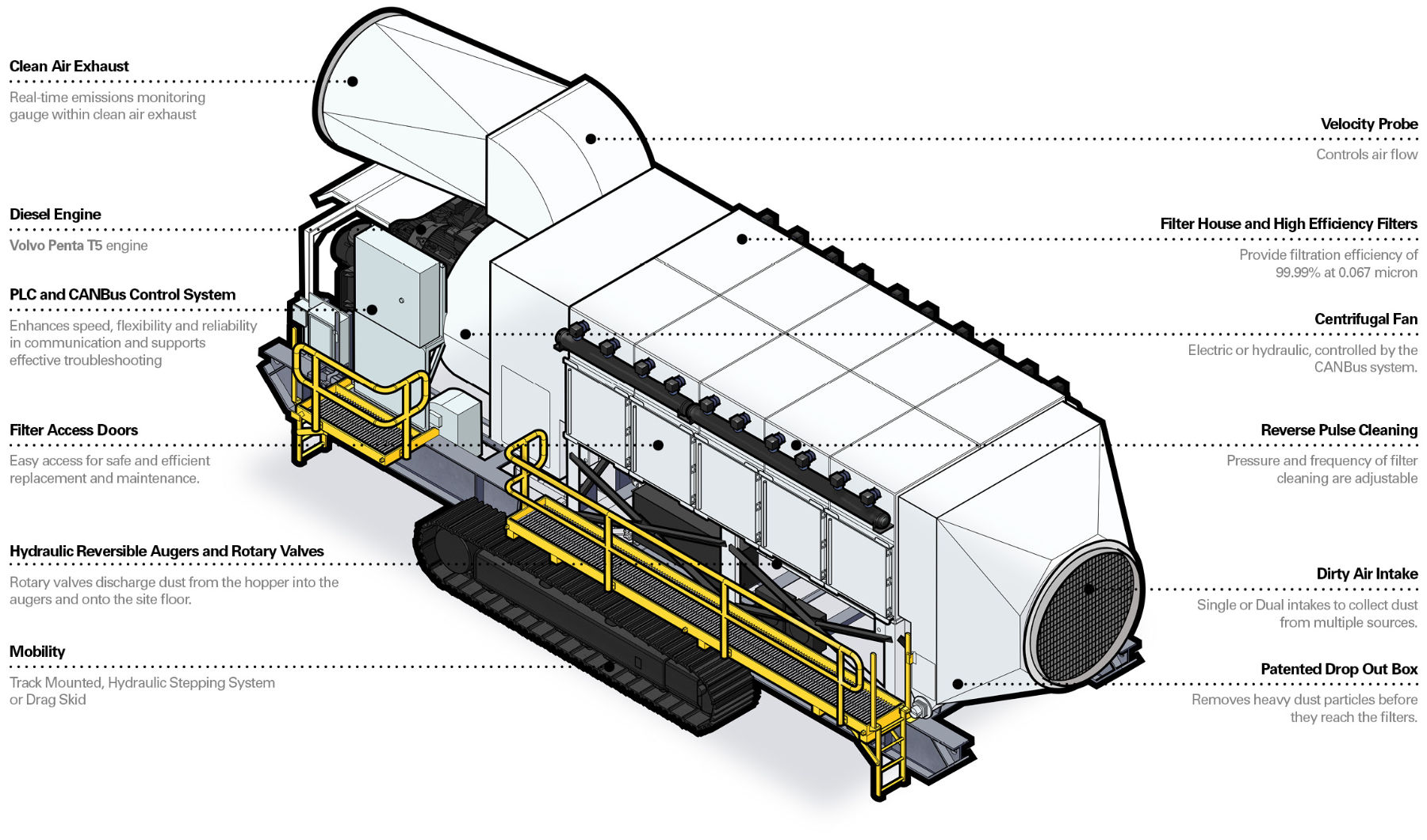
They work very much like an enormous vacuum cleaner. Whilst the principle is the same though, the scale and robustness vary just slightly.
- Air is pulled through the dirty air intake by the centrifugal fan
- Larger dust particles drop through the drop out box and are separated from the air stream
- Dust and fumes are trapped on the filters forming a cake on the surface as air passes through the filter house
- Reverse pulse filter cleaning system cleans the filters
- Dust particles are discharged from the machine via the augers and rotary valves
- The velocity probe monitors air speed and then turns the centrifugal fan up or down to maintain the air volume
- Clean air exhausts from the machine with a filtration efficiency of 99.99% at 0.067 micron
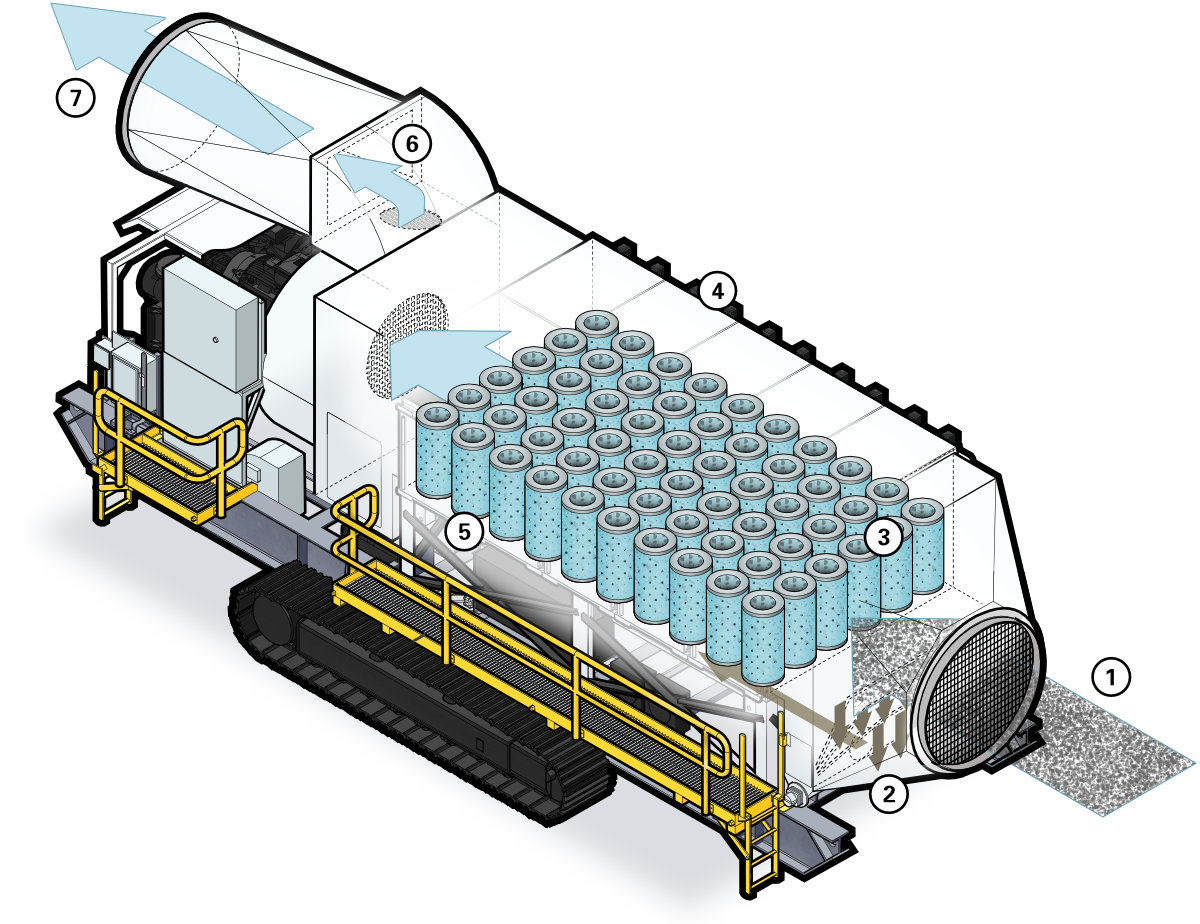
Our dust collectors also offer a few features you may not find on your typical domestic vacuum cleaner...
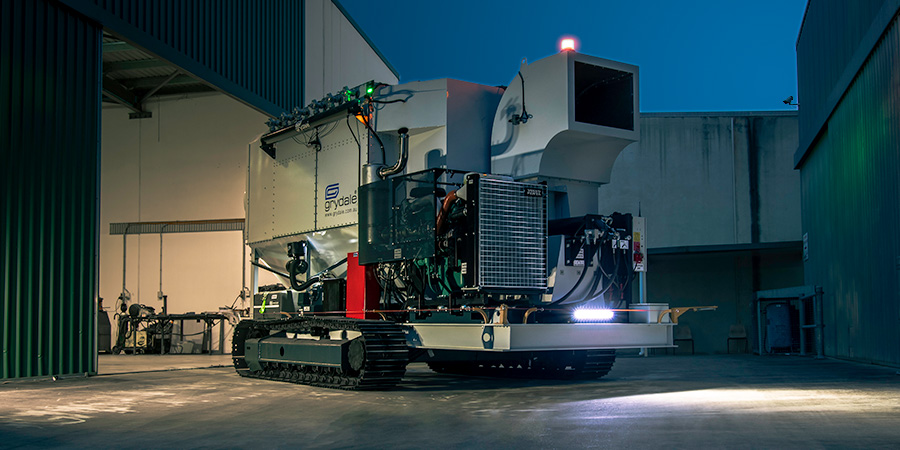
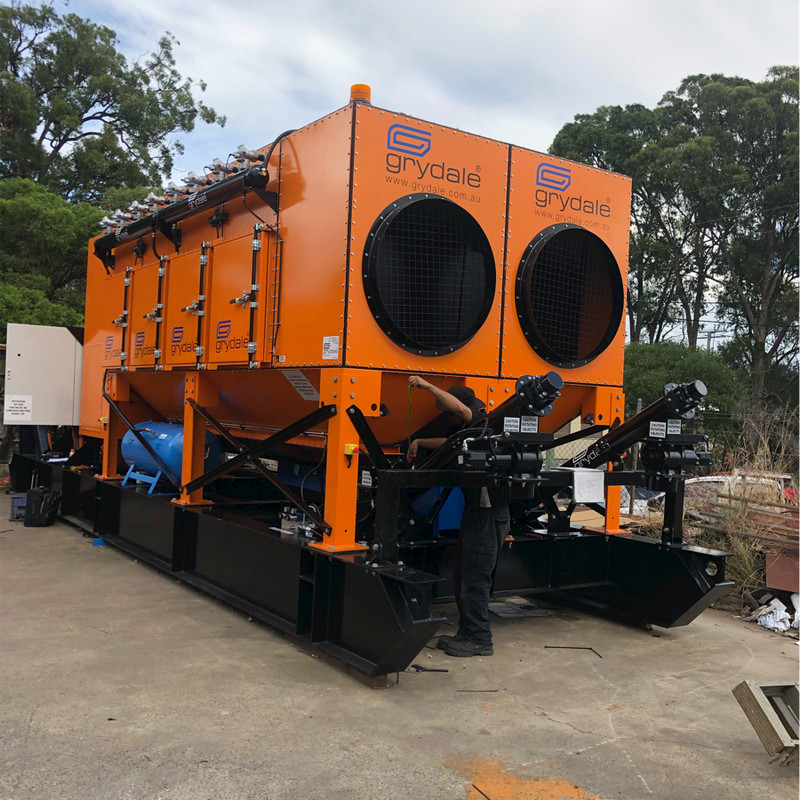
Mobility
Mobility combined with a compact integrated design – options to suit site access and applications
Tracks
Grydale hold the patent for manufacturing the only self-propelled dust collector on the market. Track units offer full mobility with variable speeds from 3 to 6kph to increase the speed and efficiency of operations. The tracks are hydraulically driven by the Volvo Penta Diesel engine and operated via remote control.
Track mobility allows dust collection units to be positioned in close proximity to dust generating activities, reducing the volume of air requiring treatment and improving the efficiency of whole site operations.
Track units are driven using remote control and are able to move and operate alongside excavation equipment such as road headers and in tunnelling are typically used for bench excavation and cross passages to provide effective dust collection at source where mobility and manoeuvrability is key.
Hydraulic stepping system
The hydraulic stepping system powers four legs that lift the units up while a pair of skates help to move the unit forward and backwards. Movement can be repeated to achieve the desired travel distance.
Drag skids
The skid can be dragged using the four towing points at each end of the machine or moved by crane using the four lifting lugs.
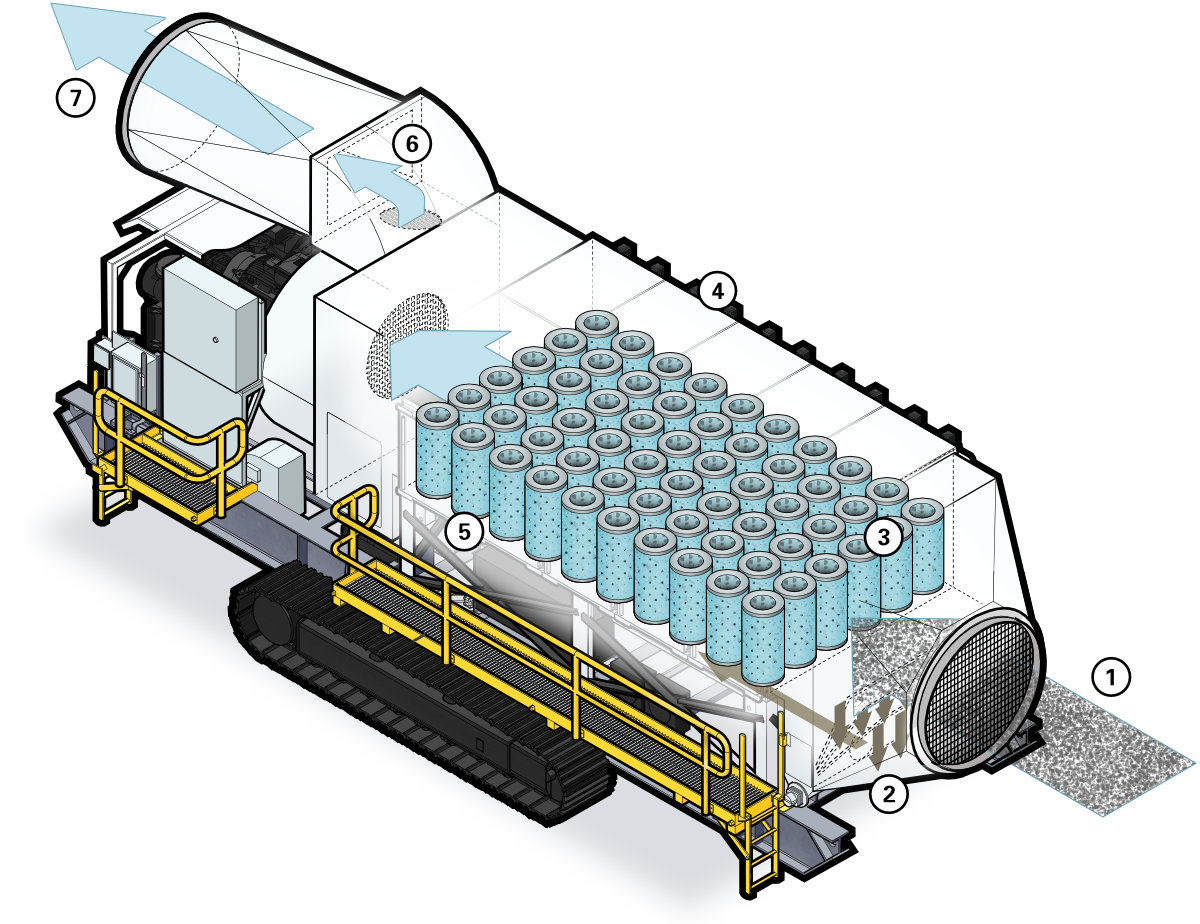
Filtration
NATA certified dust collection efficiency of 99.99% at 0.067 micron
Air intake
Available in single, dual or multiple forms, the intakes are connected to the dirty air source via ducting. For large dust volumes we recommend single intakes, while multiple intakes can be used to extract dust from multiple sources simultaneously. Flexible couplings allow the dust collector inlet to connect effectively on uneven surfaces.
Filters
High efficiency filter cartridges provide filtration of both dust and diesel particulates. Baffle plates distribute air throughout the dust collector system ensuring an even wear of filters. Filter access doors offer easy access, allowing efficient filter maintenance and maximising machine uptimes.
Reverse pulse cleaning system
All of our dust collectors have an on-board air compressor and receiver tank which feed the pneumatic system to provide reverse pulse filter cleaning. The pneumatic system’s primary function is to clean out the filters during operation to prevent dust build up on the filters.
Pressure and frequency of pulse cleaning is adjustable and helps reduce the number of filter changes required. If there is already a compressor on site, this can be utilised.
Drop out box
Our patented drop out box takes heavy dust particles and shotcrete fibres out of the air stream and discharges them through the augers and rotary valves before they hit the filters. This exclusive patented design extends filter life and allows the machine to handle extreme dust loading.
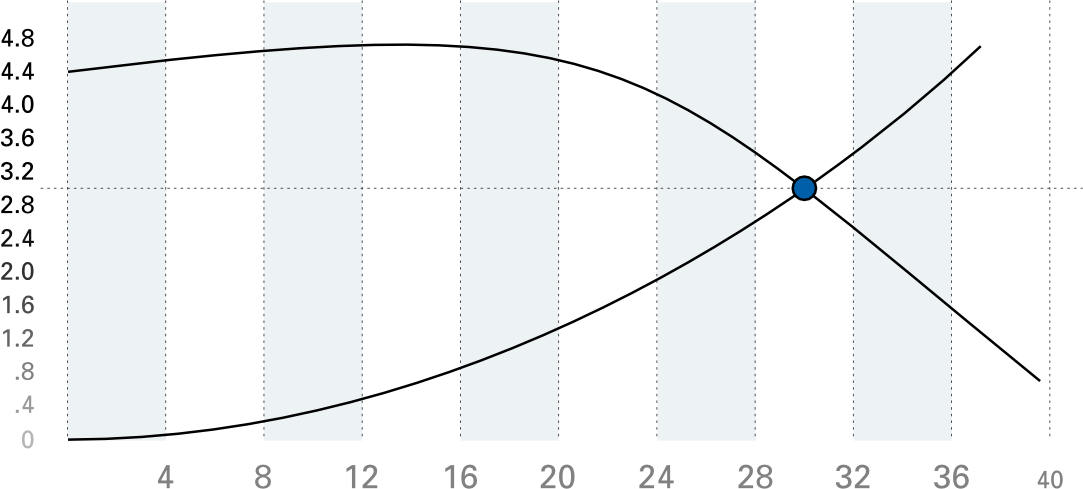
Centrifugal fan
Optimised air flow, energy efficiency and enhanced durability
Our dust collectors feature a centrifugal fan that is optimised for the application air flow and pressure requirements. Centrifugal fans offer superior energy efficiency and enhanced durability, allowing them to operate in even the most corrosive environment.
Variable speed drive and velocity probe
One of the key aspects of the JMS M-Series dust collectors is the inclusion of a Variable Speed Drive (VSD) as part of the standard configuration. The VSD is used in conjunction with a high precision air velocity probe to allow power consumption to be regulated to achieve the air volume required. This makes the units power efficient and allows projects to reduce their power consumption by up to 40%.
Fan silencer
Exhaust air passes through silencers to reduce noise pollution. We can also supply a square to round attachment allowing a vent bag to be attached to the exhaust side if required.
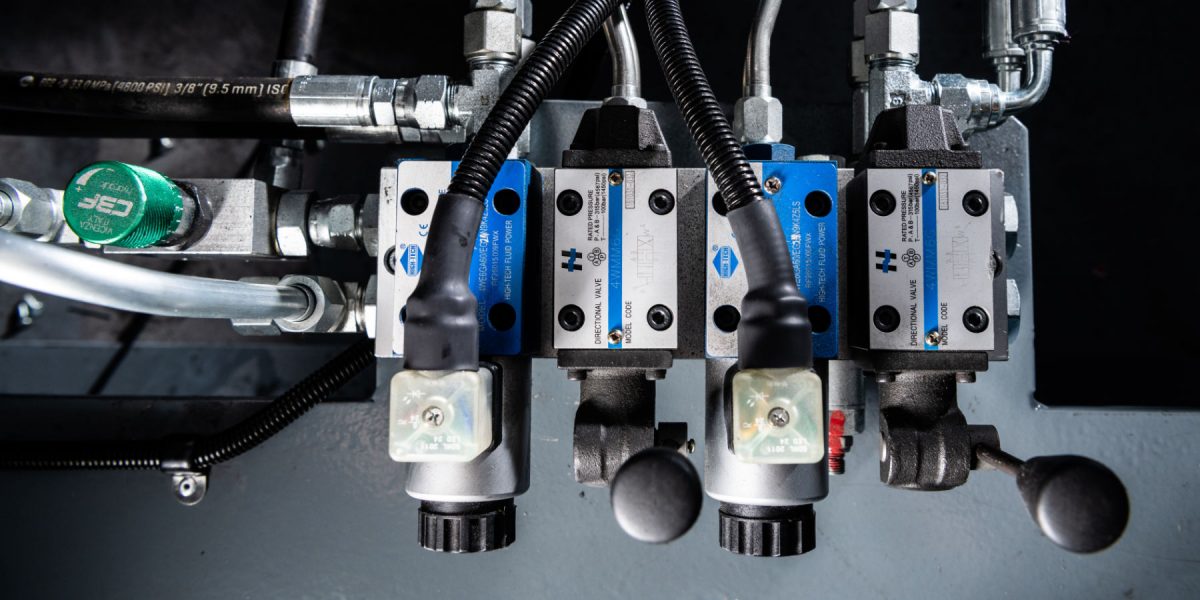
Dust discharge system
Hydraulic powered reversible augers maximise dust discharge efficiency
Hydraulic reversible auger rotary valves
Our dust collectors feature hydraulic reversible augers and stainless-steel rotary valve discharge system.
The use of hydraulics to power the augers and rotary valves maximises their efficiency whilst the ability to reverse the augers and force material through clean out hatches is key to increasing up-time in the event of product build up in the hopper. This reduces the maintenance effort and also reduces the requirement to have LV and HV electricians servicing a mechanical component. The augers also have an auto unblock feature.
Dust discharge options
Incline augers
Dust collectors with incline augers allow dust particles to be discharged to 1T bulker bags.
Slurry augers
Units are fitted with slurry augers to discharge dust from the unit into a slurry auger by the stainless-steel rotary valve and is turned into a wet slurry before being discharged onto the site floor. This helps to prevent it from reforming into dust. The slurry auger can be run off either plant water or the onboard tank water. If plant water supply is not attached the machine will discharge material as dust but will not affect operation until the water supply can be restored.
Shotcrete drop out box
The patented drop out box was designed to remove shotcrete and heavier particles from the airstream prior to entering the main filter house chamber and auger system. This design protects the filters whilst reducing the likelihood of a blockage being caused by larger particles or shotcrete fibres.
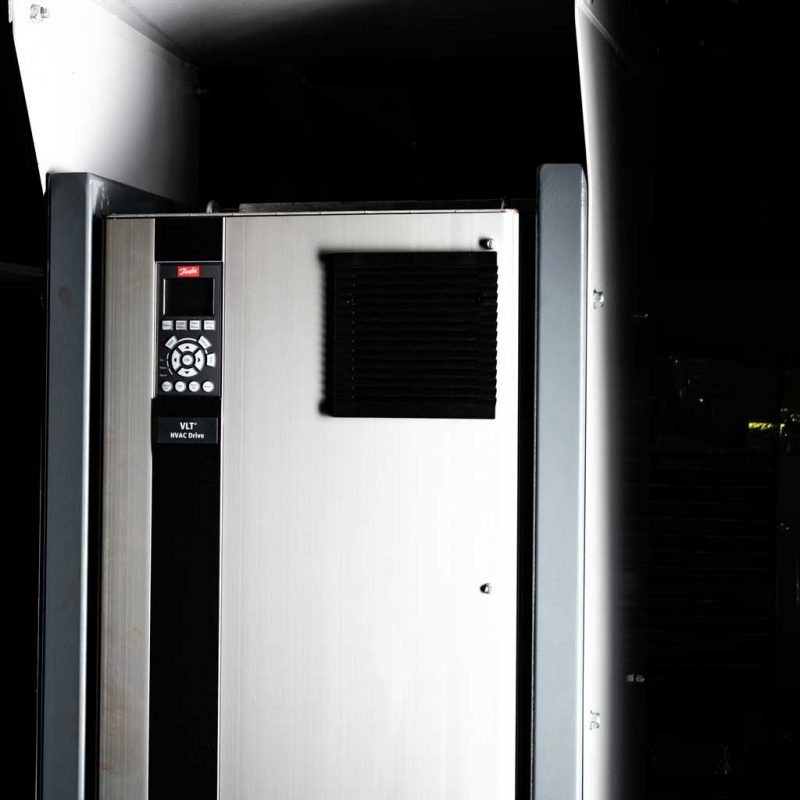
Control and monitoring options
Proprietary software facilitates ease and speed of operation.
PLC (Programmable Logic Computer)
Featuring a proprietary touch-screen display that facilitates ease of operation. The simple one-button start-up/shut-down sequence starts and stops all critical components in a programmed order, increasing the efficiency of the machine and providing additional safety measures.
The control panel allows the system to run in automatic and manual operation.
CANbus
CANBus enhances the speed, flexibility and reliability in communication and supports effective offsite troubleshooting and maintenance.
Differential and static pressure gauges
Static and differential pressure monitors are used to support operators and ensure the system is running at optimum efficiency. The static pressure monitor alerts if it’s necessary to turn the system air volume up due to a long duct run or if there’s a blockage in the ducting. The differential pressure monitor alerts the operator if filters are blocked or there are higher than normal dust loads.
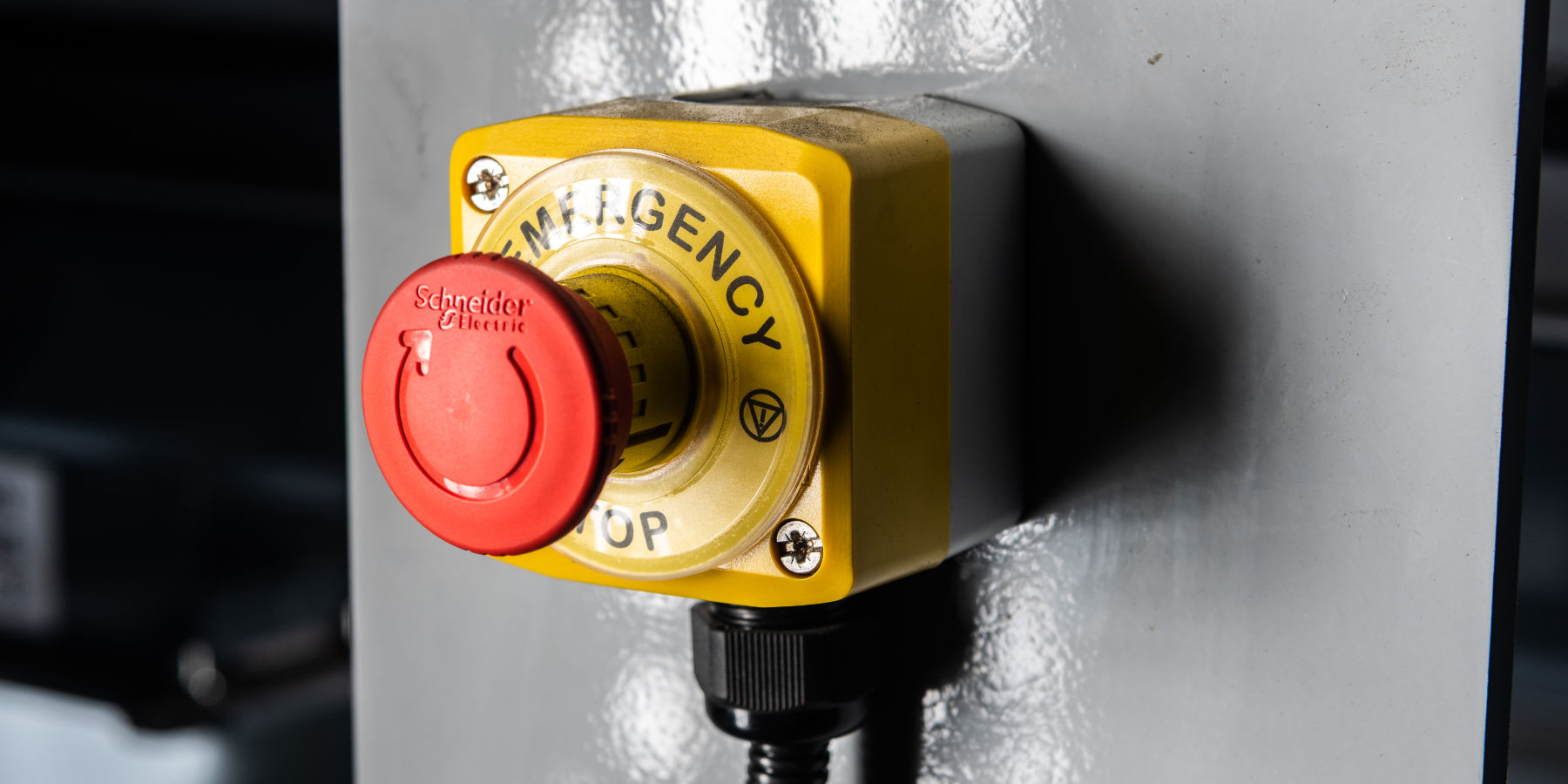
Safety features
Maximising the health and safety of workers
Our dust collectors offer a number of features that focus on maximising the health and safety of workers along with providing a safe working environment by controlling dust and fumes.
Some key safety features that are standard on our dust collectors include:
Emergency stop system
Emergency stop buttons are located around the machine. In addition, on track and stepping system units a lanyard system runs around the perimeter enabling anyone to ‘grab and kill’ the machine with immediate effect.
Split lockable isolators (diesel models)
Split starter and battery isolators allow service lights to be used when the engine is off. Full diagnostics can then be performed with minimal risk to workers.
Service lights
Maintenance lights have been fitted in key locations enabling operators and maintenance works clear visibility and / or to illuminate working spaces.
Fire protection
Fire suppression systems can be added to diesel models to ensure compliance with industry regulations.